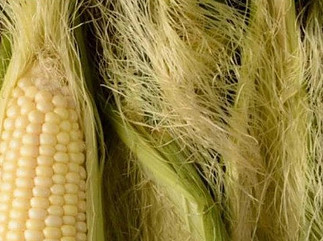
China is a powerhouse in the global amino acid market, producing approximately 60% of the world’s supply. Despite this significant contribution, the country grappled with challenges related to production efficiency and innovation, primarily stemming from underdeveloped microbial fermentation strains and a limited number of domestic patents.
Wen Tingyi, Principal Investigator at the Institute of Microbiology of the Chinese Academy of Sciences, has been pivotal in addressing these issues since joining the institute in November 2005.
Upon entering the institute, Wen quickly recognized that China was predominantly relying on traditional mutagenesis breeding techniques, which employed ultraviolet rays and chemical agents like diethyl sulfate (DES) to induce genetic mutations in microorganisms. This method was time-consuming and uncertain, requiring extensive screening to identify viable strains.
At the same time, foreign researchers were advancing rapidly with synthetic biology, allowing for precise gene editing at the DNA level. This technological gap motivated Wen to adopt gene editing techniques he learned abroad, aiming to create a platform for personalized strain transformation and innovation in industrial microorganisms.
Wen’s innovative approach involved creating a comprehensive network model of bacterial metabolic pathways by inputting all relevant genes into a computer system. This model enabled predictions about which genes needed transformation. By iteratively applying synthetic biology techniques—designing, building, testing, and learning—Wen and his team managed to increase the yield of production strains while minimizing unwanted byproducts.
In 2007, a company in Ningxia approached Wen, seeking assistance with their lysine production strain, which was yielding unsatisfactory results. The company, then a mid-level player in the domestic amino acid market, was looking to cut costs and boost profits. Utilizing the synthetic biology platform he had developed, Wen meticulously modified the strain through computer simulations, altering a total of 17 genes. This process dramatically improved the sugar-acid conversion rate and output, elevating the company’s production capabilities to international standards.
However, the landscape shifted once again. In 2005, lysine prices were around 30,000 yuan per ton, but by 2020, excess production capacity had surged, driving prices down to as low as 5,400 yuan per ton. This decline significantly impacted profit margins, leaving many companies struggling to remain viable.
Amid these challenges, Wen had a revelation. He discovered that by removing a carboxyl group from lysine, it could be transformed into 1,5-pentanediamine, a key precursor for nylon production, particularly in high-demand markets. The historical context of nylon production is notable; DuPont’s development of nylon involved 5-carbon pentamethylenediamine, later switching to a more cost-effective 6-carbon variant—hexamethylenediamine. This shift underscored the need for an alternative pathway for producing pentamethylenediamine that would not be hindered by foreign monopolies on the essential precursor, adiponitrile.
In 2021, the global nylon market surpassed 10 million tons, valued at approximately 1.5 to 1.8 trillion yuan, yet more than 90% of production was dominated by nylon 6 and nylon 66, with the latter’s precursor being largely controlled by international corporations. This left Chinese manufacturers at a disadvantage, primarily receiving only a fraction of the profits.
To tackle this issue, Wen decided to use E. coli as a production strain due to its rapid reproduction cycle of just 17 minutes, complete genetic information, and established metabolic pathways. However, E. coli inherently lacked the ability to utilize lysine for synthesizing pentamethylenediamine. Therefore, the first step was to genetically modify E. coli to incorporate foreign genes, enabling it to synthesize the desired compound.
The project faced additional challenges when it became apparent that pentamethylenediamine was cytotoxic to E. coli, inhibiting its growth once a certain concentration was reached. To overcome this, the team engineered a transport pump to expel pentamethylenediamine from the cells, allowing E. coli to thrive while continuously producing the compound.
After numerous experiments and refinements, the output of pentamethylenediamine reached world-leading levels, with nearly 100% conversion of lysine to pentamethylenediamine. Purification processes yielded a product with over 99% purity, making it suitable for industrial applications. The successful laboratory results led to plans for pilot production.
Initially, the laboratory utilized a rotary evaporator with a capacity of 5 to 20 liters, correlating to fermentation liquids produced by a 50-liter fermentation tank. However, scaling up to commercial production required significantly larger fermentation systems, presenting challenges in cost and energy efficiency. Over three years of intensive development reduced the pilot production cost of pentamethylenediamine from over 90,000 yuan to about 20,000 yuan.
By August 2020, the project culminated in the establishment of the world’s first 10,000-ton pentamethylenediamine production line in Daqing City, Heilongjiang Province. This facility utilized a distillation tower, drastically lowering production costs and improving efficiency. Following this, the team successfully polymerized pentamethylenediamine into nylon 56, producing both long and short fibers suitable for various textile applications.
Nylon 56 boasts several advantages over nylon 66, including enhanced moisture retention, ease of dyeing, flame resistance, and improved wear resistance. The resulting fabric is soft, cool to wear, and exhibits superior performance, making it ideal for activewear, underwear, and protective clothing. Collaborative ventures with leading brands have further solidified nylon 56’s market position, paving the way for its adoption in high-end products.
As demand for bio-based materials rises, Wen Tingyi’s work exemplifies a significant shift in sustainable manufacturing. The journey from corn to clothing symbolizes a broader movement towards bio-based nylon production, setting China on a path distinct from traditional petroleum-based nylon production. This innovative approach not only addresses local industry challenges but also enhances China’s competitive edge in the global market, positioning the country as a leader in sustainable textile solutions.
Source: zshq, jiemian, biotechnologyforbiofuels