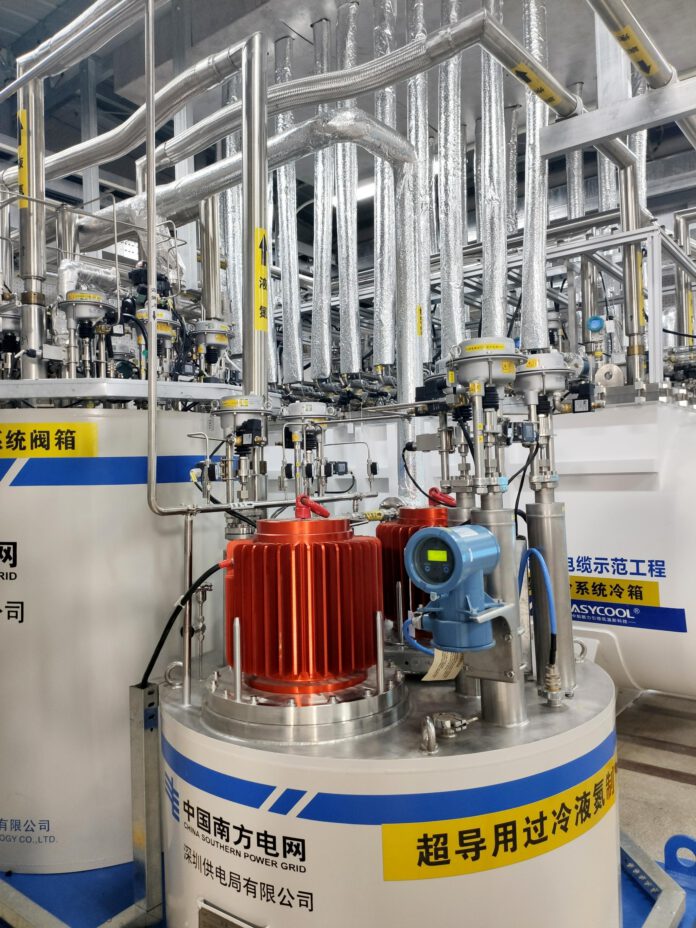
Recently, the world’s first megawatt-level high-temperature superconducting induction heating device developed by Jiangxi Lianovation was officially put into use in Heilongjiang, China. Heating from 20°C to 403°C, a traditional electric resistance furnace takes at least 9 hours while the device takes only 10 minutes and 17 seconds.
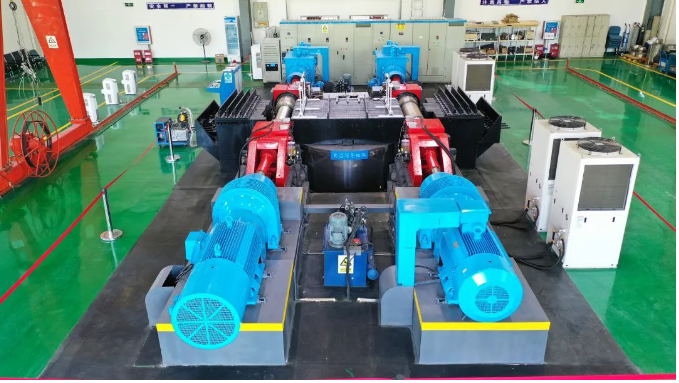
Superconducting induction heating technology refers to the superconducting magnets generating a background magnetic field, in the heating area to establish a DC air gap magnetic field, billet rotating cutting magnetic lines of force to generate eddy currents to be heated, to achieve a high depth of penetration, high energy efficiency, high heating uniformity, temperature gradient controlled by the heating method, ensuring a high quality of heating of the workpiece. The existing AC induction heating technology has limitations such as small penetration depth, low heating uniformity, and low heating efficiency.
In January 2013, to focus on the research and development of high-temperature superconducting technology, Jiangxi Lianovation cooperated with Shanghai Superconductor, Beijing Jiaotong University, and other units to establish a superconducting technology team.
At that time, there were only two industrial-scale superconducting induction heating units in the world, one each in Germany and South Korea, with a capacity of 720 kW and 300 kW respectively. However, megawatt-level superconducting heating technology has always been blank, because the key technology is in the hands of developed countries.
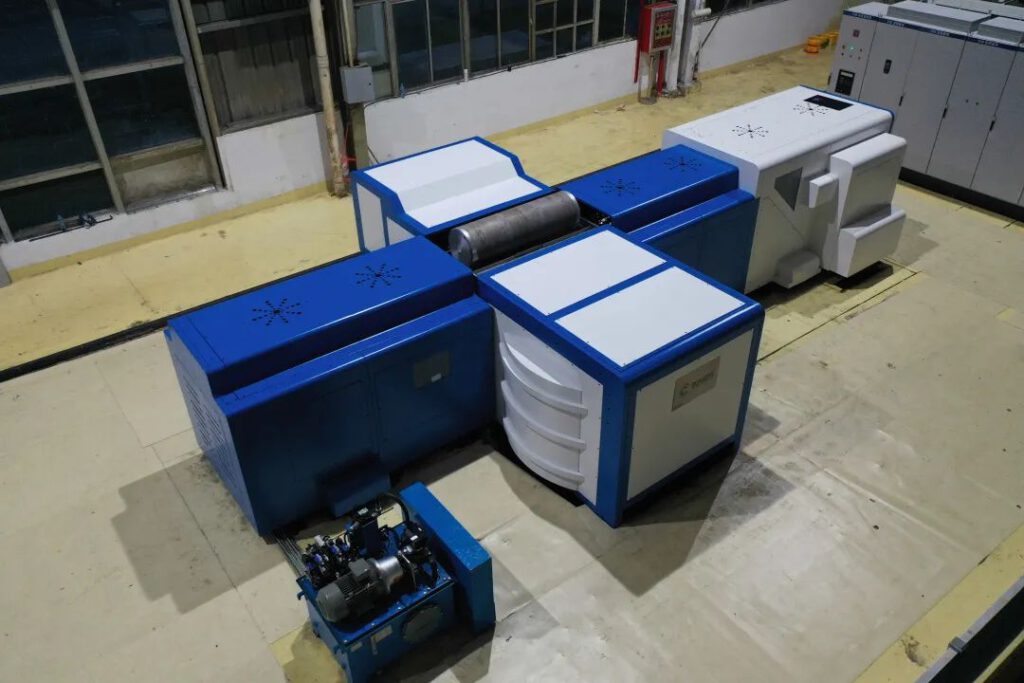
On March 8, 2019, in the test workshop of Lianovation, an aluminum rod weighing more than 500 kilograms was driven by a motor to rotate at high speed. After 18 minutes, the temperature of the aluminum rod reached the preset 450°C. The prototype test results of the megawatt-level superconducting induction heating device paved the way for today’s industrialization.
First of all, the energy conversion efficiency of the equipment is over 80%, which is more than double that of traditional heat treatment methods, which can effectively and greatly reduce the cost of metal heating; secondly, the equipment has a strong magnetic field and a good heat penetration depth, which can realize synchronous heating of the center of large-diameter metal workpieces. The temperature difference between inside and outside is small, and the performance indicators of the finished products after processing are more uniform; thirdly, the processed products can achieve gradient heating of 20-80°C per meter, which can effectively improve the performance of materials; finally, compared with traditional heating methods, there is no open flame and no heat and the device can run stably and reliably for a long time.
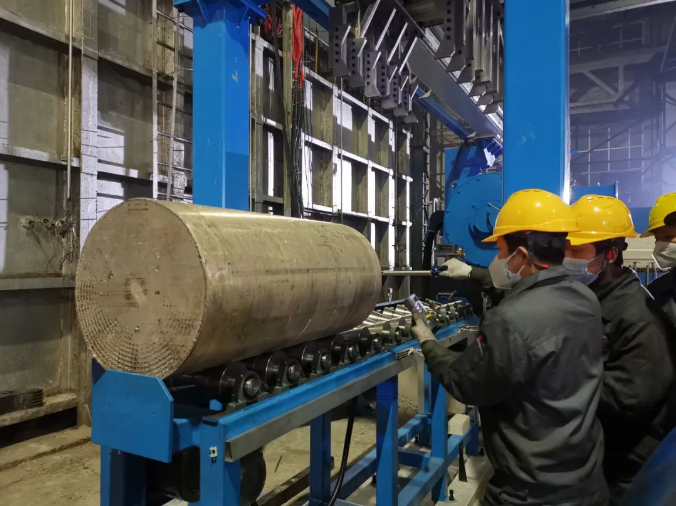
Assuming that a 2.5MW traditional industrial frequency furnace and a 1MW superconducting induction furnace have the same heating cycle per hour and the same output, take the monthly output of 3400 tons and full-load operation throughout the year as an example. According to calculations, the power consumption per ton of the superconducting induction furnace is only 150 degrees, which is 170 degrees less than the traditional power frequency furnace; the total annual operating cost is about 0.65 million dollars, which is 0.62 million dollars less than the traditional power frequency furnace.
According to statistics, the market potential of the metal calendering industry is huge. The Chinese aluminum extrusion industry alone has more than 4,000 units of large-scale heating equipment in stock, equivalent to an output value of about 8.33 billion dollars.
Lianovation takes metal processing as the entry point and has been recognized by the market in high-temperature superconducting induction heating equipment. According to reports, the company has been in in-depth contact with several large-scale state-owned enterprises processing aluminum alloys and titanium alloys for high-temperature superconducting equipment and has verified good economic benefits and energy-saving benefits brought by the device.
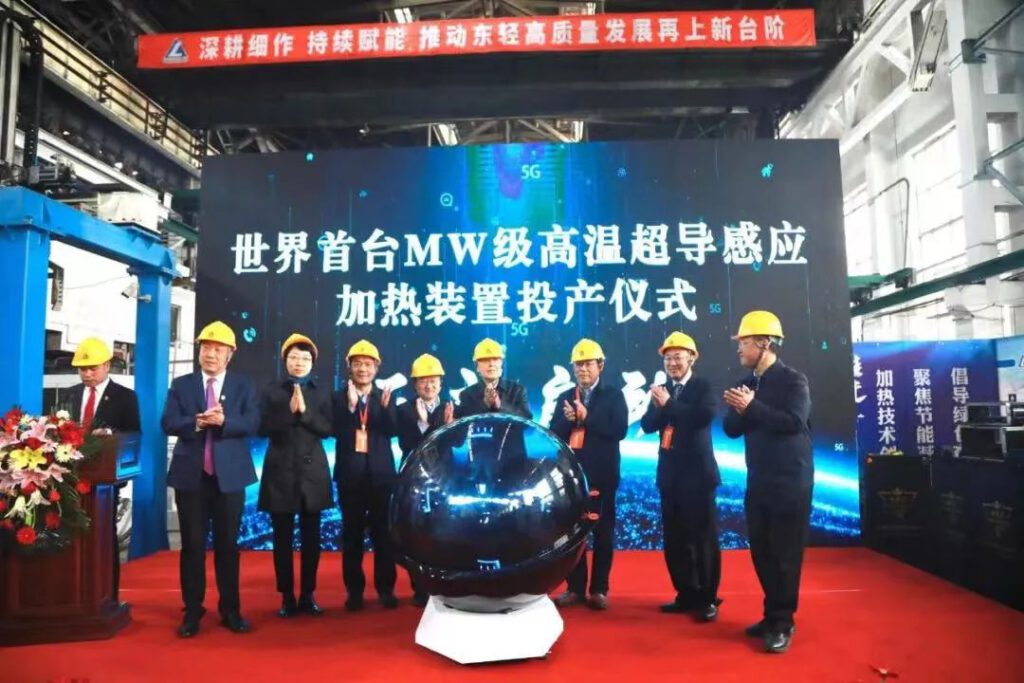
According to the plan, Lianovation’s existing production workshop can achieve an annual production capacity of 30-50 sets of equipment. After the planned superconducting industrial base is completed, it will gradually form an annual production capacity of 200 sets of magnets and superconducting induction heating equipment. As a result, it has become the largest application enterprise in the field of superconductivity in China.
According to Lianovation, in the first half of the year, the company officially entered commercialization, practicality, and industrialization. It will further optimize product quality, quickly develop key customers, make full use of existing technological advantages, and actively develop superconducting magnetic separation equipment and extended scenarios such as superconducting sewage treatment devices and superconducting single crystal silicon growth furnaces, while keeping an eye on the layout of cutting-edge technology industries such as controllable nuclear fusion and superconducting maglev trains, maintains a leading position in the industry.
(Source: lianovation, China Daily)